How 3D Printing Is Quietly Killing the Shoe Mold
- Nader Alk
- Jun 5
- 3 min read
For decades, molds have been a cornerstone of the footwear industry. From outsoles to midsoles, almost every physical prototype has traditionally relied on them. But in recent years, a quiet transformation has been unfolding. More and more brands are bypassing conventional molds during the development phase, using 3D printing instead to create functional prototypes.
The shift is not driven by hype but by real efficiency and flexibility gains.
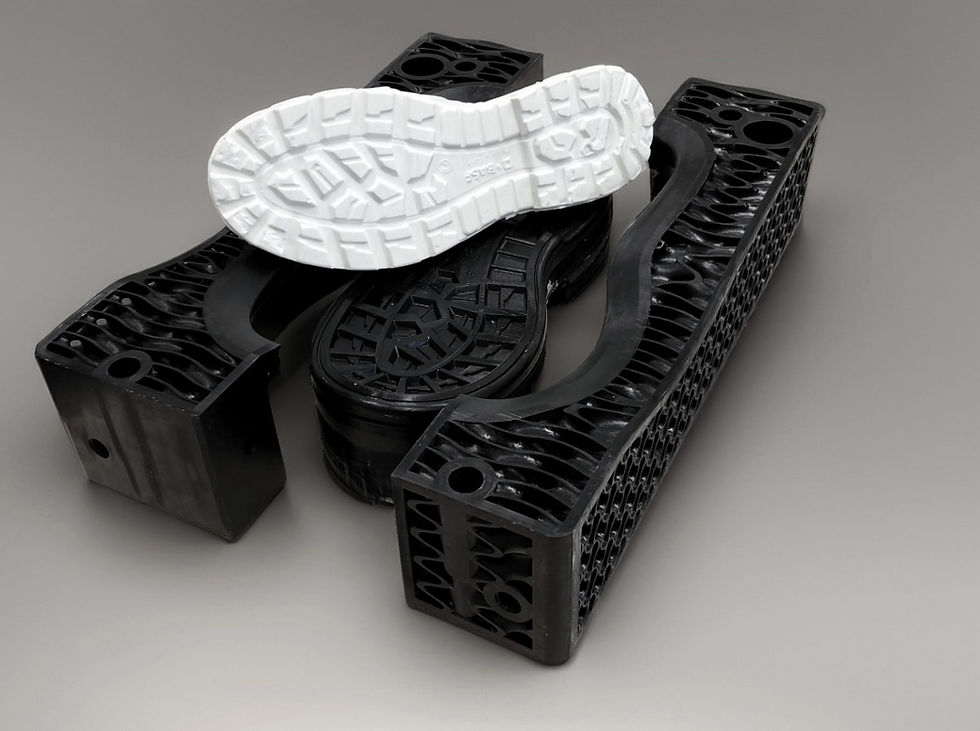
The Problem with Molds: High Cost, Low Agility
Traditional molds are expensive, slow to make, and difficult to revise. In a design culture increasingly built on rapid iteration, every structural tweak or detail refinement translates into weeks of delay and thousands of dollars in added cost.
For smaller brands or design-forward teams that prioritize creative experimentation, molds can feel less like a tool and more like a constraint.
This is where mold-free prototyping enters the picture.
Today, a digital file for a midsole or outsole structure can be transformed into a physical sample in as little as 24 to 72 hours. This direct path from CAD to object dramatically compresses development timelines. Compared to traditional molding, which can take weeks and cost thousands, 3D printing offers speed, cost-efficiency, and more importantly, the freedom to iterate as often as needed. Update the file, reprint, and move forward without remolding.
This low-barrier, high-frequency iteration model is especially well suited for lattice geometries, hollow support systems, or other complex structures that would be difficult or impossible to achieve using traditional tooling.
At the same time, printing materials are maturing. From early soft-flexible filaments to today’s elastomeric TPUs and nylon composites, the physical performance of printed prototypes has improved dramatically. Designers can now test compression, rebound, flexibility, and durability with models that closely resemble production-quality footwear.

A Deeper Shift in Prototyping Logic
Perhaps more profound than the printing itself is the shift in how brands and design teams structure their assets. Increasingly, prototyping is built on modular, parameter-driven digital models. Instead of modeling every new shoe from scratch, teams are building adjustable libraries of last shapes, midsole curves, and outsole patterns that can be recombined and fine-tuned like templates.
This approach no longer relies on one-off physical molds tailored to single designs. It depends instead on reconfigurable data and print-ready logic.
When prototyping becomes a matter of parametric design and instant fabrication, the mold begins to lose its relevance.
Mold Later, If at All
This shift is changing the traditional sequence of development. Molds are no longer the gateway to every sample. Many brands now approach them as a later-stage decision. Design, prototype, test, revise, and only when everything is finalized, commit to tooling for mass production.
In this workflow, the mold is optional. It is no longer a prerequisite but a consequence of a fully validated design.
Molds are not disappearing, but their dominance is fading. 3D printing is not replacing them outright. It is opening up a broader gray area between design and manufacturing. For teams looking to validate ideas quickly, explore novel geometries, or test structure and function in real time, this ambiguity is not a compromise. It is a strength.
As the footwear supply chain continues to evolve toward flexibility and customization, the mold is slowly stepping aside. Its successor might not be a single tool or machine but an entire ecosystem of more agile, responsive, and digital-first development methods.
Sources: materialise.com | technologyreview.com
Images: forward-am.com | voxelmatters.com
Opmerkingen